What we offer:
At Magna, you can expect an engaging and dynamic environment where you can help to develop industry-leading automotive technologies. We invest in our employees, providing them with the support and resources they need to succeed. As a member of our global team, you can expect exciting, varied responsibilities as well as a wide range of development prospects. Because we believe that your career path should be as unique as you are.
Group Summary:
Transforming mobility. Making automotive technology that is smarter, cleaner, safer and lighter. That's what we're passionate about at Magna Powertrain, and we do it by creating world-class powertrain systems. We are a premier supplier for the global automotive industry with full capabilities in design, development, testing and manufacturing of complex powertrain systems. Our name stands for quality, environmental consciousness, and safety. Innovation is what drives us and we drive innovation. Dream big and create the future of mobility at Magna Powertrain.
Job Responsibilities:
Scope of Position
- The Sr. Advanced Materials Specialist (SAMS) leads internal and external logistics planning, implementation and optimization for Magna Powertrain Shelby Twp's automotive production lines. The SAMS will work with corporate advanced manufacturing engineers and purchasing, to design all aspects of efficient, reliable supply chains, including materials procurement, supplier monitoring, electronic communication, transit, routing, packaging, storage, and lineside materials feed. They will consider new and innovative software, automation, technologies, and best use of installed equipment at the division production sites. They are responsible for strategizing supply chain improvement utilizing balance charts, a Plan for Every Part (PFEP), A3's, and Value Stream Mapping (VSM). They will submit annual cost and budget reduction plans, using advanced analytics, automation, and/or other innovative solutions. The SAMS will assist in managing personnel, methods, MRP systems and equipment for the plant's safe materials handling, receiving, warehousing and shipping. They will review and comply with deliverables of program launches to ensure timing, assigned budgets (CAPEX) and operational goals are met in accordance with Manga and customer requirements.
Minimum Requirements
- Bachelor's degree required; Supply Chain Management, Logistics, or Industrial Engineering area of study preferred.
- 6+ years experience in Automotive Supply Chain planning, w/experience as Inventory Analyst, Logistics Engineer, or Master Scheduler targeted.
- Strong understanding of Logistics principles, customs process for importing/export materials, incoterms, tax tariffs, transportation Logistics, supply chain management, and warehousing operations.
- Proven record of managing complex supply chains and driving significant cost savings.
- Expertise in data analysis, reporting, and utilizing SAP Logistics software. Staying abreast of emerging Logistics technologies and trends to identify potential applications for existing and future business needs.
- Self-motivated problem-solving leader, a team player with the ability to both lead a team and work effectively in a cross-functional team environment.
- Excellent English written and verbal communication skills, Spanish is a plus.
- Experience with Balance Charts and Value Stream Mapping (VSM) • Experience with Just-In-Time (JIT), Pull Systems and Magna Factory (MAFACT) • Working knowledge of SAP / QS / ISO / TS / IATF, GD&T, APQP and PPAP Preferred Certifications: Certified Supply Chain Professional (CSCP) or Certified in Logistics, Transportation, and Distribution (CLTD)
Additional duties and responsibilities as assigned. These duties cover only the more significant responsibilities, they are not meant to be all inclusive. Other duties may be given by Manager / Supervisor in addition to, or instead of, those listed here.
Job Specific Responsibilities
- Responsible for leading planning team and to maintain materials in support of both customer and Magna production requirements, planning for demand and engineering changes and material specific challenges, and responding/resolving any unforeseen threats to supply chain integrity.
- Work w/plant and corporate packaging engineers to design, source and procure returnable and expendable packaging, at optimal cost and storage space, for new and existing programs.
- Lead materials team set-up of customer and supplier EDI communication of forecast and daily demand requirements, and shipping notices and acknowledgement.
- Optimize work force utilization, minimize space requirements, and optimize material flow by using World Class Logistics standards (line side material presentation, warehousing, inventory levels and reorder points.)
- Travel infrequently to other Magna divisions, domestically and abroad, for launch and product specific acquisition of best practices and lessons learned, and integrate/implement applicable information into MPT Shelby Twp procedure and practice.
- Coordinate w/Magna's 3PL to contract routing for all supplier materials, ensuring a reliable and efficient supply chain that seamlessly supports plant production per customer requirements.
- Work cross-functionally with other divisional departments to design and optimize warehousing and line-side materials feed to support production while maintaining inventory targets.
- Champion maintenance of accurate inventory for finished goods, work in process, outside processing, packaging, quality hold and raw stock, with daily monitoring and correction.
- Monitor and adjust component procurement to minimize logistics costs and maintain inventory target range.
- Responsible for all dunnage issues, elimination of repacking, inventory tracking, storage location etc.
- Reviews weekly releases to determine when service orders are due and coordinates production of parts.
- Drive the development of new technologies to improve quality, efficiency and reduce cost.
- Responsible for compliance with MMOG , MAFACT, IATF and CTPAT standards.
- Responsible for Production System and synchronous material flow through lean manufacturing and 5S practices.
- Designs and schedules materials team inventory maintenance via cycle counts and physical inventories as needed.
- Conducts supplier and\\or customer visits as needed.
- Responsible for planning materials responsibilities of E.C.N. changes and launch of new products.
- Supports creation of Layered Process Audits (LPA's) to improve Materials Dept. performance.
- Participates in Kaizens and A3 projects to champions corrective actions for the Materials group.
- Leader for Pull System for manufacturing.
- Performs as the Materials Lead for MAFACT and 5S.
- Assure all safety, quality, delivery, cost, environmental, production throughput and budget practices, objectives and improvements are met. Responsible for creating KMI reports for subjects listed.
- Participates in continuous improvement activities including MAFACT, submits improvement suggestions.
General Responsibilities
These duties cover only the more significant responsibilities, they are not meant to be all inclusive. Other duties may be given by the supervisor in addition to, or instead of, those listed here.
- Actively and positively support the continued practice of Magna's Core Values.
- Must be flexible in fulfilling job responsibilities.
- Must be able to work overtime and weekends, when required.
- Initiate and embrace company change.
- Comply and participate with the Company's Continuous Improvement program.
- Practice and maintain integrity while following Magna's Charter and Constitution.
- Follow Magna's Code of Conduct and Ethics and related compliance policies. Supports and adheres to policies, procedures, and operational guidelines related to established quality management system (IATF 16949).
- Create a positive work environment by demonstrating and sharing functional/technical knowledge.
- Develop and maintain a responsive and cooperative working relationship with internal and external customers.
- Treat everyone with dignity, trust and respect.
Health, Safety & Environmental Responsibilities
- Understand applicable Environmental, Health & Safety policies and procedures in the workplace
- Observe standards for safe working conditions as outlined in the Occupational Safety and Health Administration (OHSA) as well as rules and regulations outlined in the employee handbook.
- Follows and ensure direct reports follow MIOSHA and MPTSHB safety regulations and policies, including wearing required P.P.E. (Personal Protective Equipment) and lockout/tagout.
- Commitment to quality and a safe and healthful work environment for all employees. Drive stop and fix safety culture and support "Stop Work Safe" policy.
- Complies with the designated ISO/IATF responsibilities related to effective environmental management in accordance with MPT's Environmental Management System (EMS).
- Report any hazards or unsafe conditions in a timely manner.
- Behave in a professional manner, no rough, boisterous and/or otherwise unprofessional conduct.
- Communicate, monitor and enforce Health and Safety programs and policies.
- Comply with requirements for the use or operation of machines or equipment.
- Comply with Personal Protective Equipment (PPE) requirements.
- Comply with Magna's information and data protection policies.
Global Leadership Competencies
- Think Strategically: Considers and interprets information from a variety of sources to develop and implement strategies that align with the company's long-term objectives.
- Act Decisively: Makes timely and effective decisions by interpreting guidelines and policies, ensuring that actions support the overall goals of the organization.
- Champion Change: Influences organizational and cultural change by leading initiatives that introduce new processes, technologies, and practices to enhance efficiency and productivity.
- Lead the Team: Facilitates the achievement of team results by providing clear direction, support, and motivation to team members, ensuring alignment with organizational goals.
- Inspire Others: Promotes an environment for success within teams by recognizing and rewarding achievements, fostering collaboration, and encouraging continuous improvement.
- Think Top and Bottom Line: Understanding the Business: Applies in-depth knowledge of the automotive industry, market trends, and business strategies to prioritize actions that drive profitability and growth.
- Prioritize Achievement: Leads self and others to meet high standards and achieve results by setting clear goals, monitoring progress, and holding team members accountable.
- Be Agile and Adapt: Thrives on changes and adapts to new situations by being flexible, open-minded, and proactive in addressing challenges and opportunities.
Additional Skills
- Language Skills: Requires extensive tact and communication skills (verbal and written) for direct customer communication. Ability to write routine reports and correspondence. Ability to speak effectively before groups of customers or employees of organization. Must be able to communicate fluently in both written and spoken English
- Mechanical / "Hands-on" skills: Must be comfortable with running and trouble-shooting machinery or has shown aptitude working on mechanical / electrical / pneumatic systems
- Mathematical Skills: Ability to work with mathematical concepts such as probability and statistical inference, and fundamentals of plane and solid geometry. Ability to apply concepts such as fractions, percentages, ratios and proportions to practical situations. Ability to compute rate, ratio and percent and to create and interpret graphs.
- Reasoning Skills: Ability to solve practical problems and deal with a variety of concrete variables in situations where only limited standardization exists. Ability to interpret a variety of instructions furnished in written, oral, diagram or schedule form. Ability to use problem solving when presented with problems or duties that do not have immediate answers or results.
- Computer Skills: To perform this job successfully, an individual should be proficient in: SAP MRP software for logistics and all materials applications; Microsoft Office (Word, Excel, Outlook, PowerPoint, Vizio); Microsoft Project or other Project Management software; and have navigational knowledge of Power Bi.
- Communication Skills: Must be able to relate / communicate well with people at all levels. Ability to use active listening. Ability to give positive and constructive feedback effectively.
- Problem Solving Skills: Is able to conduct individually or in team settings structured problem solving. Understands and can apply 5 Why mythology, Skillful in analysis of problems, research to identify root causes and find solutions, creativity to find robust and effective solutions to problems. Able to make decisions based on available information. Has sufficient technical knowledge to support effective problem solving.
Physical Demands
The physical demands described here are representative of those that must be met by an employee to successfully perform the essential functions of this job. Reasonable accommodation may be made to enable individuals with disabilities to perform the essential functions.
Work Environment
While performing the duties of this job, the employee is in an office setting and plant floor. The noise level in the office environment is usually low to moderate. The employee may be required to be on the production floor where they would be exposed to moving mechanical parts. The noise level in the production environment is usually low to moderate.
Awareness, Unity, Empowerment:
At Magna, we believe that a diverse workforce is critical to our success. That's why we are proud to be an equal opportunity employer. We hire on the basis of experience and qualifications, and in consideration of job requirements, regardless of, in particular, color, ancestry, religion, gender, origin, sexual orientation, age, citizenship, marital status, disability or gender identity. Magna takes the privacy of your personal information seriously. We discourage you from sending applications via email or traditional mail to comply with GDPR requirements and your local Data Privacy Law.
Worker Type:
Regular / Permanent
Group:
Magna Powertrain
Top Skills
What We Do
We are a mobility company that innovates like a start-up and thinks like a technology company. This helps us anticipate change in one of the most complex industries in the world and respond quickly. We depend on a team of 171,000 dynamic, entrepreneurial-minded employees in an environment where great ideas flourish. Our presence spans 343 manufacturing operations and 88 product development, engineering and sales centers in 29 countries.
We understand that you need a career as unique as you are. Whether you want to advance your existing expertise or try something completely different, we are committed to your growth.
Why Work With Us
At Magna, our engineering team is advancing mobility for everyone and everything. Joining this team means being a part of the design, development, and manufacturing of the world’s most advanced mobility technology. Innovations that move families, shape communities, and improve lives. You can follow your passions and shape your own career path.
Gallery
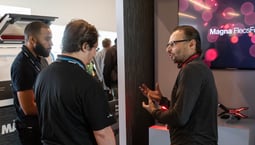
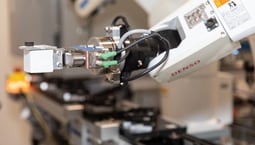
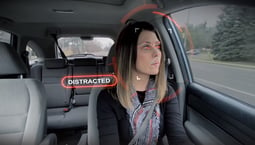
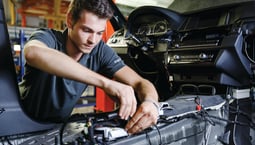
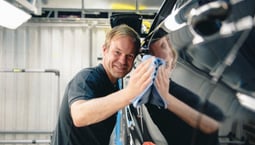
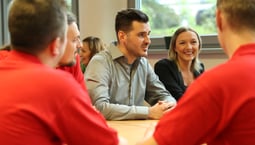
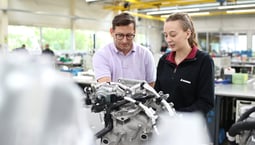
Magna International Teams
Magna International Offices
Hybrid Workspace
Employees engage in a combination of remote and on-site work.
Majority of roles are hybrid with flexibility. Please speak with our recruiting team for specific details on hybrid work.